Angels Aircraft is an aerospace technology company dedicated to transforming how aerospace innovation happens. Instead of altering the mission itself, we focus on revolutionizing how it is accomplished. Our approach centers on streamlining aerospace production more efficiently by integrating proven technologies and techniques from adjacent industries.
We reimagine mission execution by leveraging different technology sets, asking: How would we achieve these goals if we had access to entirely new tools? Beyond just envisioning this future, we are committed to making it a reality through continuous iteration. Iteration is the key to optimization—accelerating the build process allows us to validate concepts faster, standardize assemblies, and eliminate unnecessary complexity.
This blog marks the beginning of a series where I will explore what sets Angels Aircraft apart from other aerospace technology companies. Stay tuned as we dive into the innovations reshaping the industry.
Across the manufacturing industry, complexity often drives up costs. The more intricate a mission or product, the more expensive it becomes to produce. This cost scales with factors such as size, number of parts, precision requirements, and tolerance control. Additionally, cost tends to be inversely proportional to quantity due to learning curves—an in-depth topic I may cover in a future blog. (For now, you can reference the conceptual cost curve I’ve included in the image or look up more information on the topic.)
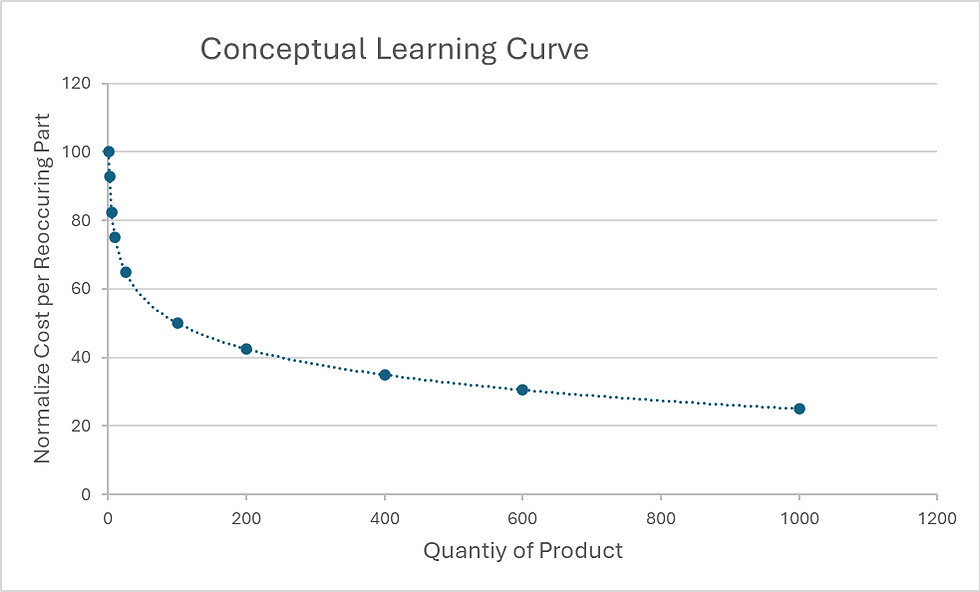
Manufacturing techniques and production quantities also play a critical role in cost efficiency. Large industries have invested heavily in research and development to refine highly efficient manufacturing methods. At Angels Aircraft, we aim to leverage these advancements by adopting materials, techniques, and processes from adjacent markets. By doing so, we reduce the cost of delivering specific capabilities or significantly enhance capabilities at the same cost. Our goal is to achieve a balance between the two.
There are several key technology groupings that can benefit from this approach. Today, I’ll focus on design and production implementation for structures, propulsion systems, avionics systems, and ground support systems, while also introducing LEAN manufacturing—specifically, the high-level concepts I find most valuable. In this blog series, we’ll take deeper dives into methodologies and trade spaces as Angels Aircraft works toward making our vision a reality.
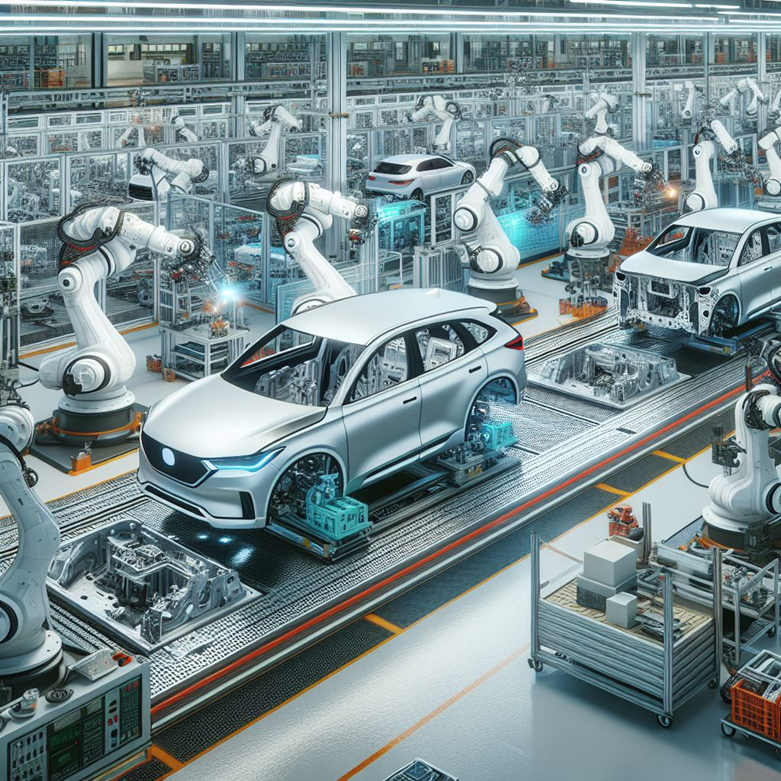
LEAN Manufacturing
To transform our vision into reality, we must first establish a conceptual framework and align our manufacturing approach accordingly. The ultimate goal is to achieve steady-state production, much like an automotive assembly line. This method is the most efficient because work cells focus on executing specific tasks within a defined time frame.
For steady-state production to function smoothly, all steps must be synchronized to maintain a uniform Takt time—the time allotted for each task in the production cycle. You can think of it like the time each robotic arm has to work on a car in an automated assembly line. While batch processing can be integrated into this system, the key is maintaining an inventory system that seamlessly feeds individual components into the production flow without disruptions. This principle should guide the design and setup of any efficient production facility.
In upcoming blogs, we’ll explore these concepts further, diving into the methodologies that will shape Angels Aircraft’s journey toward revolutionizing aerospace manufacturing. Stay tuned.
When designing an efficient production line, assembly paths should be organized strategically. The components with the highest frequency of use and the greatest number of parts should be placed closest to the production line, while larger, less frequently used parts should be positioned farther away. Every movement within the production process costs money, so the most frequently moved items should follow the shortest, most direct paths.
Scaling Inventory and Quality Control with Production Growth
In the early stages of production, inventory is typically stored in a single location, often alongside quality control and incoming inspections. However, as production scales toward steady-state manufacturing, inventory and inspections must be decentralized and integrated into work cells, where each task is performed.
Once work cells are established, the next step is streamlining operations within each cell. In most cases, human workers—not robots—carry out these tasks. A well-organized work cell mirrors the efficiency of the overall factory, just on a smaller scale.
Optimizing Work Cell Layout
Each step in a work cell’s process should be:
Clearly defined (through work instructions).
Easily verifiable (via a traveler document).
Obvious and intuitive for the technician.
To illustrate the importance of accessibility, I like to use a basketball dribbling analogy: If a technician cannot reach what they need by pivoting on one foot, it is too far away.
Additionally, only essential tools should be available. Overstuffed toolboxes slow down efficiency. Anyone who has worked on cars knows how frustrating it is to dig through a drawer full of sockets only to realize the 7/16-inch socket—the one you need—is missing. Instead, use shadow boxing:
Lay out all the necessary tools on a table.
Create a shadow outline around each tool.
This makes it instantly clear when something is missing.
This same principle applies to recurring materials, kits, and fixtures. Work cells should be set up so that:
Recurring inventory is easily accessible from the aisle for quick restocking.
Tools and fixtures are positioned against the wall, as they should remain within the work cell.
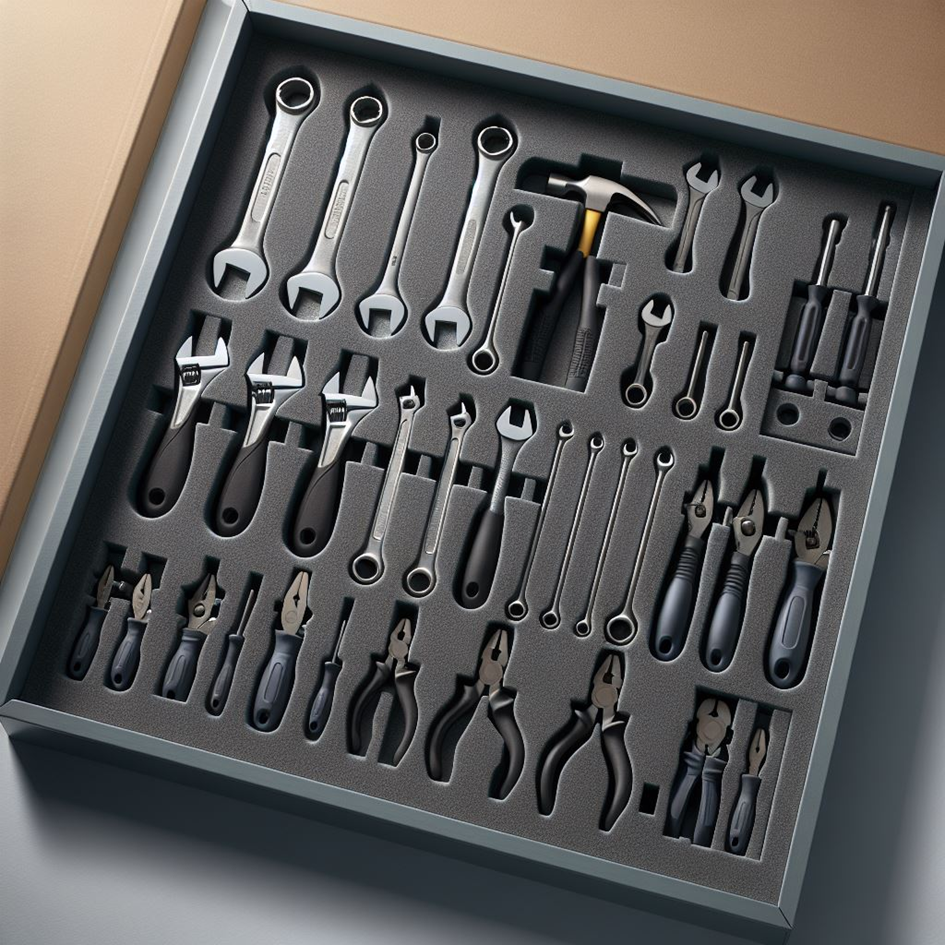
A Simple Test for LEAN Work Cells
Many companies claim to follow LEAN principles, but a quick glance at their work cell setup can reveal the truth. Here’s a simple test:
Are essential tools within easy reach? If not, efficiency is suffering.
Are there enough garbage cans? In a truly LEAN system, workers shouldn’t have to walk far to dispose of waste, meaning you’ll often see more garbage cans than you’d expect.
By following these principles, Angels Aircraft is building an efficient, scalable, and optimized manufacturing system—one that balances speed, organization, and cost-effectiveness.
Structures
Structures have been my passion for 20+ years. Initially, I thought my career would lead me to the automotive industry, but instead, I went into aerospace—eventually going into NewSpace before circling back to explore aerospace technologies again. Throughout my career, I’ve learned valuable lessons: not all technologies are good, some should be avoided, and others offer more efficient learning paths that bring ideas to reality faster and more cost-effectively.
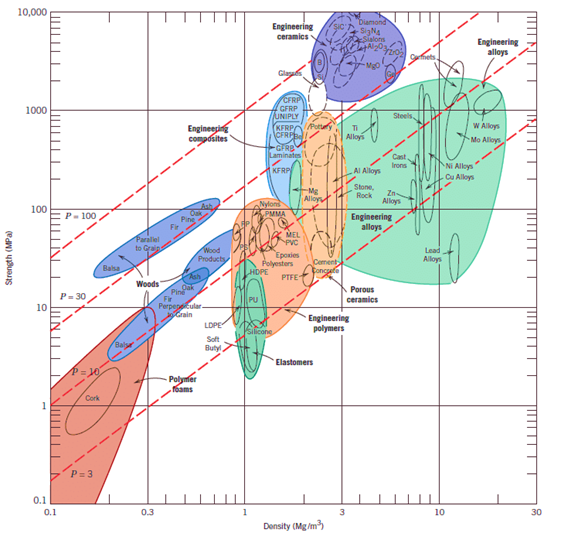
Materials: Understanding Cost vs. Performance
A fundamental aspect of structures is understanding the materials you’re working with. A well-documented material can be slightly modified, but every change requires rigorous validation. While metals and fasteners have well-established databases, adhesives, plastics, and specialized parts often lack comprehensive statistical data. Modifying a material system without this data means applying overly conservative knockdowns to ensure reliability—leading to heavier and costlier designs.
It’s also critical to assess cost versus performance in terms of dollars per pound for your product. Fasteners, for example, can quickly become prohibitively expensive or difficult to source if they are highly specialized. Using commonly available parts is key, reserving high-performance fasteners ("Hallelujah bolts") only for extreme cases. Even then, these bolts often introduce new failure mechanisms like stress corrosion and material incompatibilities, meaning they should be designed out of the system as soon as possible.
The fastest way to ensure that simulation models align with real-world materials is to use well-documented data sets. In aerospace composites, these are called allowable data sets. Without them, engineers risk designing an aircraft that is overly conservative and unnecessarily heavy.
Additionally, when considering developing a new material, it’s essential to evaluate return on investment. In composites, for example, stiffer materials are generally more expensive. If increased stiffness doesn’t lead to weight reduction, higher payload capacity, or significantly cheaper manufacturing, investing in “better” materials may drive up costs without delivering meaningful benefits.
Unitization: Reducing Part Count to Lower Costs
Reducing part count has an exponential impact on decreasing vehicle costs. Fewer parts mean:
Fewer drawings
Fewer specifications
Fewer qualification tests
Fewer handling events
Fewer assembly steps
However, larger parts come with trade-offs. They require:
Significant capital investment to manufacture.
Higher risk, as a single failed large part can be more costly.
Increased manufacturing complexity.
Finding the optimal balance between part count and manufacturing constraints is key. This requires understanding both material properties and production techniques to determine the ideal number of parts for a given design.
Designing for Production Efficiency
Every additional part increases setup and teardown costs. These costs aren’t just physical tooling changes but also include:
Printing work instructions
Tracking and scanning travelers
Moving parts to inspection
Preparing manufacturing kits
Setting up and breaking down workspaces
The most efficient production method is a steady-state production line, where parts continuously flow without interruptions. If steady-state production isn’t feasible, batch processing should be implemented, ensuring that similar parts are manufactured together. Additionally, all production should be organized using a LEAN workspace layout to minimize inefficiencies.
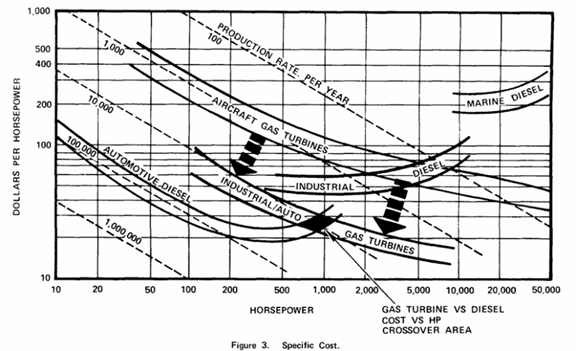
Propulsion Systems
Aerospace propulsion systems must be extremely reliable in the environments they operate in. This necessity has led to the widespread use of proven, time-tested technologies in commercial aviation.
For small aircraft, carbureted engines and leaded fuel remain prevalent. This is because new technologies often introduce additional risks and complexity, while traditional air-cooled, mechanically simple engines are well understood and highly optimized. The same principle applies to jet engines—qualifying a new engine for manned flight is a long, difficult process, making industry adoption slow.
When developing new propulsion technologies, I believe the key factors are:
Redundancy – Ensuring backup systems are in place to enhance reliability.
Data Collection – Capturing extensive data to characterize engine performance.
Autonomous Testing – Gathering information in an automated and non-invasive manner.
The cost of this validation and testing should be absorbed by the manufacturer and amortized across the production run—this is already standard practice for aircraft engines.
Angels Aircraft: A Different Approach to Propulsion
At Angels Aircraft, we take a unique approach to propulsion system design, much like our philosophy with structures:
Unitizing Assemblies – Simplifying components to reduce cost and complexity from the start.
Material Standardization – Selecting common shafts, compressors, stators, and housings to avoid supply chain bottlenecks and long lead times.
Part & Material Commonality – Using standardized geometries and materials to improve failure analysis, scalability, and simulation efficiency.
Aircraft engines have known high-complexity parts, especially in the hot section. While these areas require specialized attention, the rest of the engine should be easy to maintain and replace.
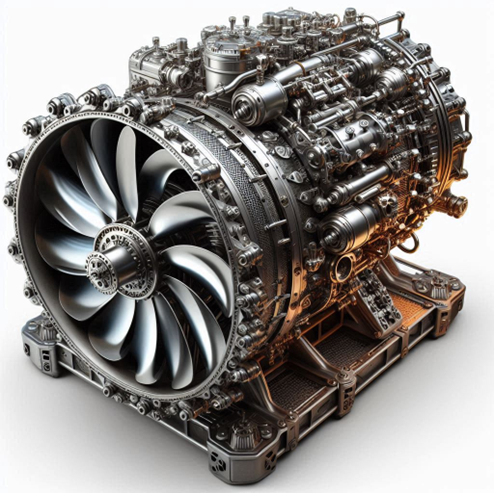
Modular & Rapid-Replaceable Design
We are designing our engines to be fully modular and rapidly replaceable—an engine swap should take 30 minutes or less. Initially, this will be a manual process, but the long-term goal is a fully automated engine replacement system that can be executed directly on the flight line.
When it comes to engine servicing, our priority is minimizing downtime. Instead of grounding an aircraft for full engine inspections, we are designing systems that allow quick removal and replacement of only the critical components—keeping the rest of the aircraft in operation.
Avionic Systems
Much like engines, avionics systems rely on a proven, highly reliable technological backbone. Even in unmanned systems, the architecture remains fundamentally similar—a central flight computer processes sensor data, manages controls, and directs system operations. When redundancy is needed, the typical solution is to add another computer, doubling the associated wiring and harness complexity. The same principle applies to control actuators and, in some cases, fluid systems.
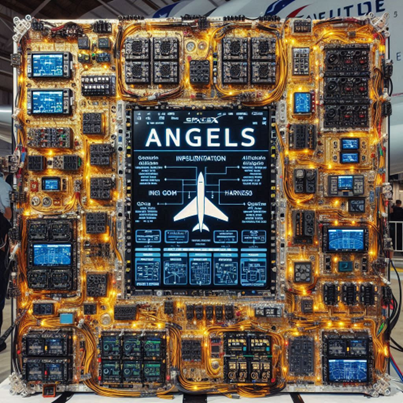
Angels Aircraft: A New Avionics Architecture
At Angels Aircraft, we are developing a more advanced and efficient avionics architecture. Instead of dedicating each CPU to a single function, we implement a networked system where multiple CPUs share tasks dynamically. Our approach includes:
Distributed Processing – All onboard CPUs are networked, allowing multiple instances of flight software to run simultaneously.
Hierarchical Functionality – Data intake, processing, and control execution are distributed across the system rather than handled by a single, isolated unit.
Optimized Digital Control System – By managing data loops and power loops within a digital thread, we gain a more robust, adaptable, and efficient system.
Key Advantages of Our Approach
Increased Reliability – Tasks are shared across multiple computational assets, preventing single-point failures.
Reduced Complexity & Weight – Simplifying data connections and harnessing eliminates unnecessary wiring, making the system lighter and more maintainable.
Enhanced Data Analytics & Optimization – By leveraging real-time data analytics, we can optimize flight performance, improve navigation, and enhance mission execution.
By integrating redundancy at the system level rather than through excessive hardware duplication, Angels Aircraft is creating more streamlined, resilient, and intelligent avionics systems for the future of aerospace.
Swarms vs. Single Platforms
Swarms inherently offer built-in redundancy, as well as cost savings driven by learning curves and production efficiencies. However, this approach is only viable when high-value assets can be distributed and when the mission can be simplified accordingly.
By deploying a swarm of autonomous vehicles, each capable of:
Self-navigation
Fuel management, including autonomous refueling
Coordinated mission execution
we enable persistent surveillance and dynamic mission adaptation.
Key Advantages of the Swarm Approach
Distributed High-Value Assets – Instead of concentrating expensive sensors, data links, and munitions on a single platform, they can be strategically dispersed across swarm members.
Enhanced Situational Awareness – Lower-cost sensors can collaborate to create a 3D view of the battlespace, enable direction finding, and facilitate distributed capabilities (e.g., simultaneous surveillance and electronic warfare).
Modular & Interchangeable Systems – Since swarm vehicles share identical core systems, they offer interchangeability—a white-tail aircraft (one without a specific mission system) can serve as a spare parts repository to maximize fleet uptime.
This scalable, adaptable, and resilient approach provides a cost-effective alternative to traditional single-platform systems, while enhancing operational effectiveness in complex environments.

Ground Support Systems
Ground support systems encompass all operations required to maintain and prepare an aircraft while it is on the ground. This includes everything from post-flight inspections to preparing the vehicle for its next mission. The key challenge is minimizing the effort needed to return an aircraft to flight-ready status efficiently.
At Angels Aircraft, we aim to automate as many of these processes as possible—reducing the reliance on skilled support staff and minimizing turnaround time between flights. Our approach focuses on streamlining:
Automated Inspections & Diagnostics – Using advanced data analytics to monitor system performance and detect potential issues early.
Sensor Calibration – Ensuring avionics and mission-critical instruments remain precise without requiring manual intervention.
Fuel & Environmental Systems Management – Handling refueling, defueling, and environmental control autonomously, reducing risk and increasing efficiency.
Armament Handling & System Checks – Automating munitions loading and verifying system integrity for mission readiness.
Modular Component Swaps – Designing systems that allow for rapid part replacement, especially for components that require in-depth inspections or are prone to wear.
Scalability & Safety
Many of these automated support solutions are already employed in rocket operations, where fuel handling and system checks are performed remotely due to hazardous environments. We propose scaling these technologies to aircraft servicing, enabling faster, safer, and more efficient ground support operations.
By integrating automation and intelligent diagnostics, Angels Aircraft is redefining ground support—optimizing aircraft readiness while reducing costs and operational complexity.
In Conclusion
Today’s discussion covered several key aspects of aerospace technology and production optimization, focusing on how Angels Aircraft is redefining traditional aerospace methodologies. We explored LEAN manufacturing principles, emphasizing efficient production layouts, part standardization, and streamlined workflows to reduce costs and complexity. The importance of unitization, or reducing part count, was highlighted as a critical factor in optimizing manufacturing efficiency and minimizing failure points.
We also examined key aerospace subsystems, including structures, propulsion, avionics, and ground support systems. For structures, we discussed material selection, cost-performance trade-offs, and designing with manufacturability in mind. In propulsion, we explored simplifying supply chains, increasing component commonality, and designing engines for rapid maintenance and replacement. Avionic systems were reimagined with a networked, distributed computing architecture to improve reliability and reduce hardware complexity. Finally, ground support automation was proposed to enhance aircraft turnaround times, leveraging autonomous inspections, fueling, and maintenance—similar to techniques already used in rocket servicing.
Additionally, we covered the advantages of swarm-based systems over single-platform designs, emphasizing redundancy, modularity, and cost efficiency. By distributing high-value assets across multiple vehicles, swarms offer enhanced situational awareness, mission flexibility, and logistical resilience. Overall, Angels Aircraft is taking a holistic, efficiency-driven approach to aerospace technology, aiming to disrupt traditional models with scalable, cost-effective, and highly adaptable solutions.
I would love to hear your comments on this. What areas would you like to be expanded, do you agree with what was said. I encourage alternative viewpoints on this as well!
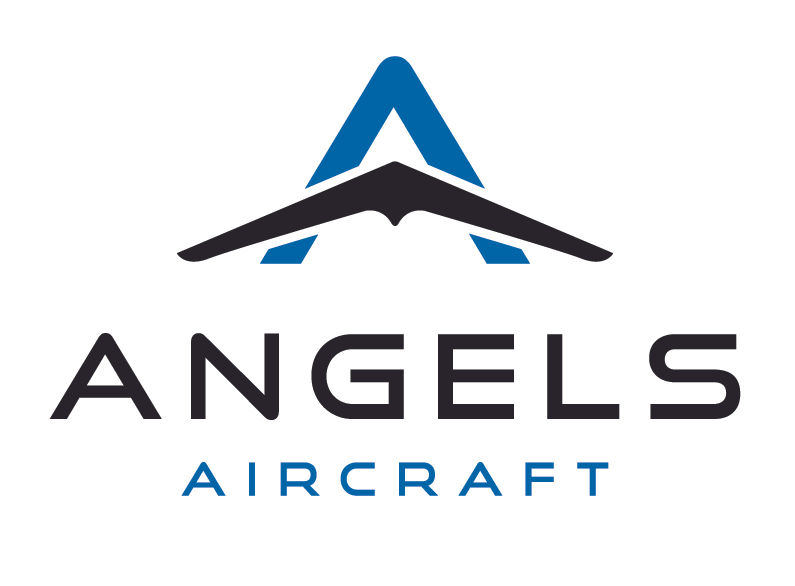
Commentaires